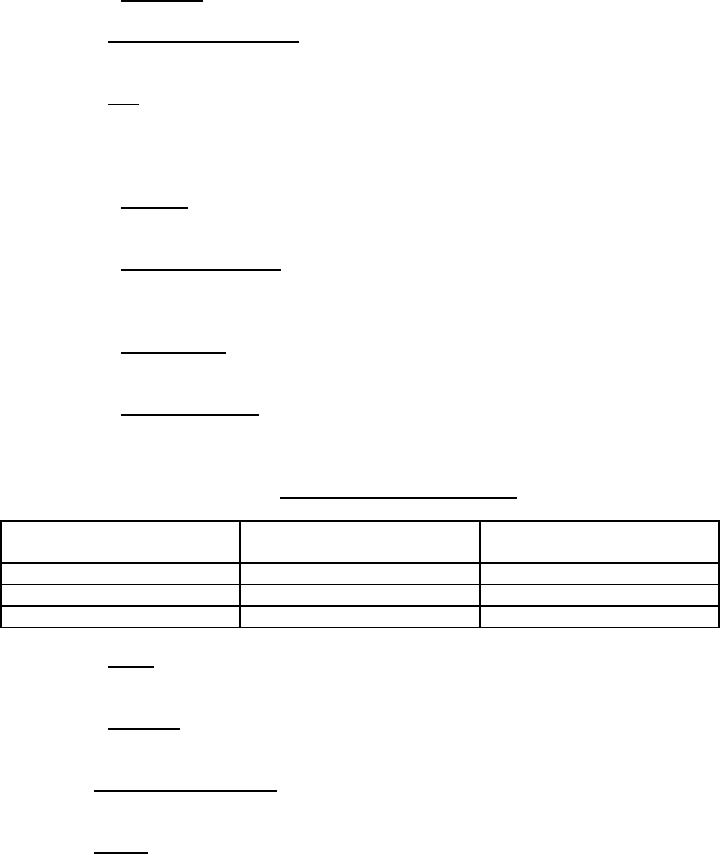
MIL-DTL-5500G
part of the cap shall project outside the overall dimension indicated.
3.3.1.1 Valve stem. The cap shall fit with MIL-PRF-6164 valve stem.
3.3.2 Shell and swivel seat plate. Material used in the shell and swivel seat plate shall be
as specified in MS20813.
3.3.3 Seat. The valve seat material shall be in accordance with MIL-PRF-6855, class 2,
type A, grade 60 or 80, or approved equivalent, that is resistant to hydraulic oil, conforming to
MIL-PRF-83282 and shall be suitably bonded to the swivel seat to withstand service usage
without separation of the bond.
3.3.3.1 Resistant. The material shall be resistant to abrasion to prevent disintegration
under pull-up tests or during normal service usage.
3.3.3.2 Compression resistant. The material shall have suitable compression set
resistance and flexibility at all operating temperatures between -65° to 160°F (-54° to 71°C) to
seal all operating pressures up to 5,000 psi with maximum wrench torque of 30 inch-pounds.
3.3.3.3 Homogeneous. The material shall be homogeneous to insure consistent swell,
strength, and hardness characteristics throughout the entire batch.
3.3.3.4 Physical properties. When subjected to accelerated aging in either air or
hydraulic oil, conforming to MIL-PRF-83282, the tensile strength, elongation, and hardness
characteristics of material shall not change more than the values indicated in TABLE I.
TABLE I. Seat material physical properties.
PROPERTY
CHANGE INCREASE
PERCENT DECREASE
(MAX)
(MAX)
Tensile strength
-
20
Elongation
-
30
Hardness shore durometer
10
10
3.3.4 Finish. Finish shall be as specified in MS20813. The swivel seat need not be
finished.
3.3.5 Assembly. The bonded valve seat assembly shall swivel freely in the housing after
assembly, but shall not fall out during normal service handling or usage.
3.4 Proof and burst pressures. Caps shall withstand a proof pressure of 10,000 psi and a
burst pressure of 20,000 psi.
3.5 Pull-up. The caps shall withstand 30 pull-ups at a wrench torque of 50 inch-pounds.
Ten of these pull-ups shall be after the caps have been exposed a minimum of 72 hours to a
temperature of -65°F (-54°C).
3
For Parts Inquires submit RFQ to Parts Hangar, Inc.
© Copyright 2015 Integrated Publishing, Inc.
A Service Disabled Veteran Owned Small Business