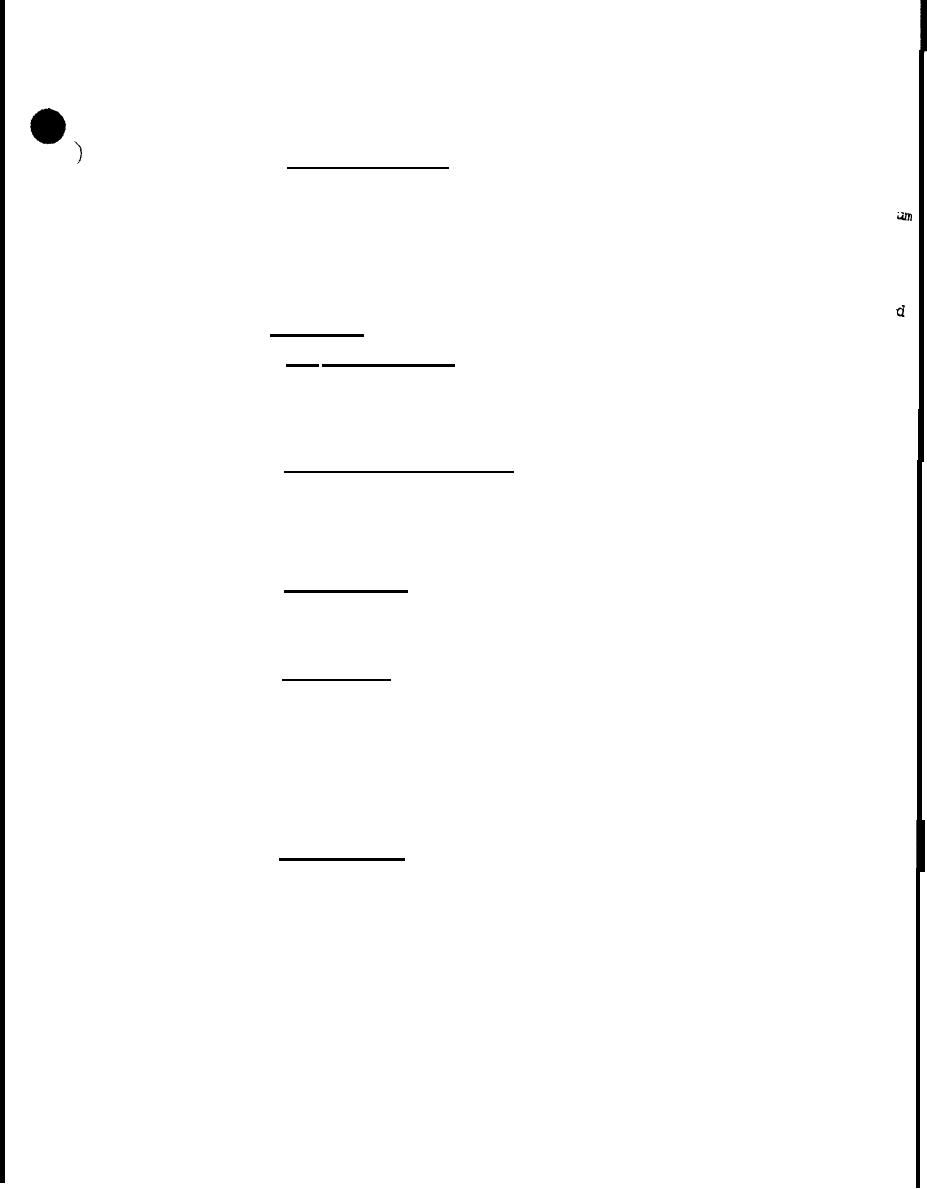
MIL-H-8890(ASG)
-
4.6.7 Mission- profile tests. - Becauae of the advance in air vehicle per -
formance with the accompanying complexity in requirements, purely steady steady-state
condition tests will be insufficient to provide proof that the component will
operate satisfactorily in service. In such cases, it will be necessary to con-
duct tests simulating the sequence, magnitude, and duration of the conditions
which the component is expected to encounter during the course of an actual air
vehicle mission. Mission-profile tests may combine high and low temperature,
rapid warmup, thermal shock, altitude, vibration, acceleration, shock, perform-
ance, and endurance tests as one integrated test, as specified in the detail speci-
fication.
4.7 Test methods. -
4.7.1 Examination of product. - When specified in the detail specification,
the component shall be carefully examined to determine conformance with the
requirements of the applicable specifications for weight, workmanship, marking, s
envelope, defects, and conformance of dimensions of detail parts to manufacturer
drawings. All critical dimensions of the specimen shall be recorded in the pre-
production and production teat reports.
4.7.2 Performance verification tests. - The performance verification tests
are preproduction and production tests as specified herein and shall be specified
in the detail specification. They shall be conducted at room temperature prior
to conducting other tests in order to estsblish initial performance. The same
tests shall be repeated at the intervals and conditions specified in the prepro-
duction and production tests and the results recorded and compared with the initial
tests.
4.7.3 External leakage. - During the course of all the tests listed in this
specifications external leakage, other than a slight wetting insufficient to form
a drop through static seals, shall be cause for rejection. Where external dynamic
seals are utilised, permissible leakage past such seals shall be no greater than
specified in the detail specification.
4.7.4 Proof pressure. - When specified in the. detail specification the
component shall be pressure tested at proof pressure. The proof pressure shall
be applied while the component is stabilized at a fluid temperate Of 450° F and
0
o
an ambient temperature from 450 F to 635 F. The rate-of-pressure rise shall not
exceed 25,000 pounds per square inch (psi) per minute. A hand pump may be used if
desired. The proof pressure shall be applied at least two successive times and
held 2 minutes for each pressure application. The component shall be operated in
its normal function between applications of the test pressure. There shall be no
evidence of external leakage, other the a slight wetting insufficient to form a
drop, or permanent set. Components which require varying test pressures in diff-
erent elements may have these pressures applied either separately or simultaneously,
4.7.5 Internal leakage. - When specified in the detail specification, the
component shall be tested for internal leakage. The internal leakage tests shall
be performed with the component held in the position most conducive to leakage.
The component shall be tested for leakage by applying 5 psi, 50 percent of working
pressure, and working pressure for a period of 5 minutes each, unless otherwise
specified in the detail specification. The leakage measurement period shall begin
2 minutes after the application of the required pressure, The component shall be
13
For Parts Inquires submit RFQ to Parts Hangar, Inc.
© Copyright 2015 Integrated Publishing, Inc.
A Service Disabled Veteran Owned Small Business